CASO 3
Industria: Inyección de Plástico
Tipo de maquinaria: 50 sistemas hidráulicos con componentes de alta precisión (servo válvulas, válvulas proporcionales, bombas y motores hidráulicos).
Problema: anualmente daño en componentes hidráulicos como servos y reemplazo de las piezas ( 20 válvulas promedio anual ), cambio de 5 bombas hidráulicas por desgaste, ocasionando paros frecuentes de producción y costo elevado por reposición de refacciones hidráulicas, cambios constantes de lubricantes y costo por disposición de los mismos.
Solución: programa análisis de aceite a unidades hidráulicas para control predictivo , implementación de filtros de respiración higroscópicos desecantes para restringir fuentes de contaminación y humedad por vía de respiración en unidad hidráulica. Instalación de unidad de filtración de aceite a una micra de tamaño con absorción de humedad para limpieza constante de lubricante para procuración de los componentes de alta precisión en maquinaria.
Beneficios: incremento en confiabilidad de maquinaria, productividad y eficiencia de la empresa, disminución de consumo de componentes hidráulicos (por ejemplo de 20 servos que se consumían al año, después de 5 años se reemplaza la primer servoválvula), el desgaste y consumos en bombas hidráulicas se disminuyó notablemente. El tiempo de vida del lubricante se alargó de uno a 6 años.
CASO 4
Industria: Química
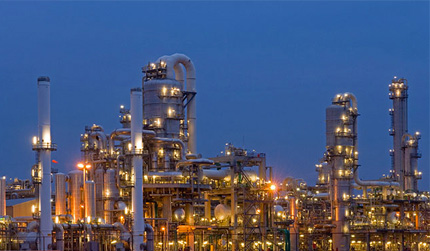
Tipo de maquinaria: bomba centrífuga de rodamientos, volumen de aceite= 2 litros, ISO 150.
Problema: área de extrema humedad y contaminación del medio ambiente, por proceso normal de planta existe un tanque de agua caliente el cual rebosa el fluido contenido hacia la parte inferior de este donde se encuentran las bombas centrífugas siendo una fuente de contaminación.
Debido al ingreso de humedad y agua en sistema de lubricación de bomba centrífuga, existía daño en rodamientos que requieren su cambio al menos 3 veces al año, de igual forma se realiza el cambio de carga de aceite y sellos mecánicos y cada paro por daño en rodamientos representa 6 horas pérdidas de producción.
Solución: implementar un sistema cerrado en sistema de lubricación mediante un indicador constante de nivel ( sistema cerrado) y un filtro de respiración desecante con cámara de expansión para procurar así un sistema cerrado para control de ingreso de contaminantes, agua y humedad hacia la carcasa del sistema de lubricación en la bomba de proceso.
Beneficios: incremento en confiabilidad de bomba de proceso, productividad y eficiencia de la empresa, el tiempo de vida del lubricante se alargó de 3 meses a 3 años, el rodamiento no ha sido cambiado en 3 años ni el sello mecánico, no ha existido reposición del nivel de aceite.